Industrial robots are multi-joint manipulators or multi-degrees of freedom machine devices that are oriented toward the industrial field. They can perform work automatically, and are machines that rely on their own power and control capabilities to achieve various functions. It can accept human command, or it can be run according to pre-programmed procedures. Modern industrial robots can also act according to the principles established by artificial intelligence technology. 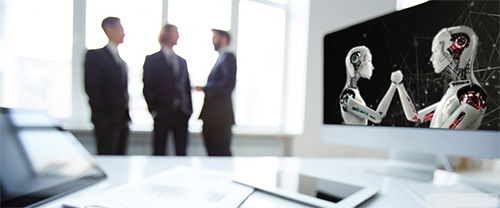
The robot control system is the brain of the robot and is the main factor that determines the function and performance of the robot. The main task of the industrial robot control technology is to control the movement position, posture and trajectory of the industrial robot in the working space, the operation sequence and the time of the operation and the like. Has the characteristics of simple programming, software menu operation, friendly human-computer interface, online operation prompts and easy to use. The advantages of industrial robots 1. Cost savings Robots can operate 24 hours. For example, if the product is taken out and placed on a conveyor belt or a receiving platform, only one person can watch or one person can watch two or more machines at the same time, which effectively saves labor costs. In addition, the use of industrial robots to operate the model, automatic assembly line can save plant sites, make the whole plant planning smaller and more compact and exquisite. The description of the robot, please modify it. 2. High production efficiency The time it takes for a robot to produce a product is fixed. Within the same life cycle, the use of robots is also fixed in output and does not change. And each model's product production time is fixed, the product's yield is also high, the use of robot production is more in line with the interests of the boss. 3, high safety factor The use of robotic production, can be greater to protect the safety of workers. There will be no accidents caused by work negligence or fatigue. Physiological fatigue is more likely to occur at night in a survival workshop where shifts are needed, leading to safety accidents and the use of robots to ensure safe production. In addition, some of the more dangerous types of work, the use of industrial robot operation, higher accuracy, higher stability, stronger security, can guarantee the safety of personnel. 4, to facilitate management In the past, it is difficult to accurately ensure the daily production of the company, because there will always be some employees lazy. As a supervisor, there are a lot of things every day. It is difficult to catch employees at all times and do something well. After using robots to produce, the number of employees is reduced, and employee management is more convenient. Types of Industrial Robots 1. Mobile Robots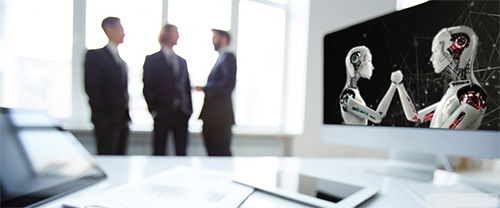
The mobile robot (AGV) is a type of industrial robot. It is controlled by a computer and has the functions of mobile, automatic navigation, multi-sensor control, network interaction, etc. It can be widely used in machinery, electronics, textiles, cigarettes, medical, food, Functions such as flexible handling and transmission in papermaking and other industries are also used for automated three-dimensional warehouses, flexible processing systems, and flexible assembly systems (with AGV as an active assembly platform); they can also be used as transportation vehicles in the delivery of goods at stations, airports, and post offices. . 2. Spot welding robots Welding robots have the characteristics of stable performance, large working space, fast moving speed and strong load capacity. The welding quality is obviously better than manual welding, which greatly improves the productivity of spot welding operations. 3, arc welding robot Arc welding robot is mainly used in various types of automotive parts welding production. In this field, international large-scale industrial robot manufacturers mainly provide unit products to complete equipment suppliers. 4. Laser Processing Robots Laser processing robots use robotics in laser processing to achieve more flexible laser processing operations through high-precision industrial robots. The system operates online through the teach pendant and can also be programmed offline. The system produces a model of the workpiece by automatic detection of the machined workpiece, which in turn generates the machining curve, and can also be directly processed using CAD data. Can be used for laser surface treatment of workpieces, drilling, welding and mold repair. 5. Vacuum robots Vacuum robots are robots that work in a vacuum environment. They are mainly used in the semiconductor industry to realize the transmission of wafers in vacuum chambers. Vacuum robots are difficult to import, are limited, use a large amount, and have strong versatility. They have become a key component that restricts the progress of R&D of semiconductor equipment and the competitiveness of the entire product. Moreover, foreign countries have rigorously reviewed Chinese buyers and belonged to the embargoed product catalog. Vacuum manipulators have become a serious problem that restricts the manufacturing of semiconductor equipment in China. Direct-drive vacuum robot technology belongs to original innovation technology. 6. Clean Robots Clean robots are industrial robots that are used in a clean environment. With the continuous improvement of production technology, the requirements for the production environment are increasingly demanding. Many modern industrial products are required to be produced in a clean environment. Clean robots are the key equipment needed for production in a clean environment. Industrial robot applications Typical applications for industrial robots include welding, painting, assembly, collection and placement (eg, packaging, palletizing, and SMT), product inspection, and testing; all work is done with efficiency, durability, speed, and accuracy. 1. The conveyor line robot and conveyor line logistics automation system is mainly composed of the following components: automated conveyor line, robot system, automated three-dimensional storage supply system, main line control system, bar code data collection system, product automation test system, production line monitoring / Dispatch / Management System. Robot and conveyor line logistics automation system can be applied to building materials, home appliances, electronics, chemical fiber, automobile, food and other industries. 2. Glue The robot gluing station is a robot application system developed and developed by the robot center. It mainly includes robots, glue supply systems, glue spreaders, workstation control systems, and other peripheral ancillary equipment. The workstation has a high degree of automation and is applicable to many varieties and mass production. It can be widely used in automotive windshields, automobile and motorcycle headlights, building materials doors and windows, solar photovoltaic cell coating and other industries. 3, welding The system is generally more commonly used gas metal arc welding (MIG, MAG, CO2 welding) or non-gas metal arc welding (TIG, plasma arc welding) method. Equipment generally includes: welding power supply, welding torch and wire feeding mechanism, welding robot system and corresponding welding software and other auxiliary equipment. Automatic robot welding workstations can be widely used in railway, aerospace, military, metallurgy, automotive, electrical and other industries. 4. The automatic crating robot automatic packing and palletizing workstation is an integrated system, which includes industrial robots, controllers, programmers, robot hand grippers, automatic demolition/stacking machines, pallet transport and positioning equipment and yards.åž› mode software. It is also equipped with automatic weighing, labeling and inspection and communication systems, and is connected with the production control system to form a complete integrated packaging production line. Automatic robot packing and palletizing workstations can be applied to building materials, home appliances, electronics, chemical fiber, automobiles, food and other industries. 5. The automatic welding shaft automatic welding station is used for welding various workpieces with the rotating shaft as the base (a number of cantilevers are placed on it). It consists of a welding robot, a rotary duplex positioner (a number of stations) and a fixture. The use of different fixtures in the same workstation can realize automatic welding of various types of shafts, and the relative position accuracy of the welding is high. Can be widely used in high-quality, high-precision welding of various types of workpieces based on the shaft, suitable for electric power, electrical, mechanical, automotive and other industries.
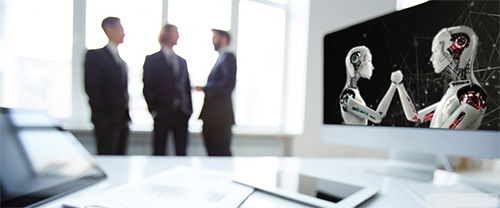
The robot control system is the brain of the robot and is the main factor that determines the function and performance of the robot. The main task of the industrial robot control technology is to control the movement position, posture and trajectory of the industrial robot in the working space, the operation sequence and the time of the operation and the like. Has the characteristics of simple programming, software menu operation, friendly human-computer interface, online operation prompts and easy to use. The advantages of industrial robots 1. Cost savings Robots can operate 24 hours. For example, if the product is taken out and placed on a conveyor belt or a receiving platform, only one person can watch or one person can watch two or more machines at the same time, which effectively saves labor costs. In addition, the use of industrial robots to operate the model, automatic assembly line can save plant sites, make the whole plant planning smaller and more compact and exquisite. The description of the robot, please modify it. 2. High production efficiency The time it takes for a robot to produce a product is fixed. Within the same life cycle, the use of robots is also fixed in output and does not change. And each model's product production time is fixed, the product's yield is also high, the use of robot production is more in line with the interests of the boss. 3, high safety factor The use of robotic production, can be greater to protect the safety of workers. There will be no accidents caused by work negligence or fatigue. Physiological fatigue is more likely to occur at night in a survival workshop where shifts are needed, leading to safety accidents and the use of robots to ensure safe production. In addition, some of the more dangerous types of work, the use of industrial robot operation, higher accuracy, higher stability, stronger security, can guarantee the safety of personnel. 4, to facilitate management In the past, it is difficult to accurately ensure the daily production of the company, because there will always be some employees lazy. As a supervisor, there are a lot of things every day. It is difficult to catch employees at all times and do something well. After using robots to produce, the number of employees is reduced, and employee management is more convenient. Types of Industrial Robots 1. Mobile Robots
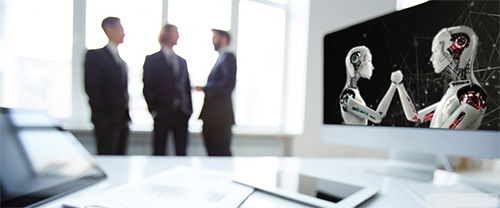
The mobile robot (AGV) is a type of industrial robot. It is controlled by a computer and has the functions of mobile, automatic navigation, multi-sensor control, network interaction, etc. It can be widely used in machinery, electronics, textiles, cigarettes, medical, food, Functions such as flexible handling and transmission in papermaking and other industries are also used for automated three-dimensional warehouses, flexible processing systems, and flexible assembly systems (with AGV as an active assembly platform); they can also be used as transportation vehicles in the delivery of goods at stations, airports, and post offices. . 2. Spot welding robots Welding robots have the characteristics of stable performance, large working space, fast moving speed and strong load capacity. The welding quality is obviously better than manual welding, which greatly improves the productivity of spot welding operations. 3, arc welding robot Arc welding robot is mainly used in various types of automotive parts welding production. In this field, international large-scale industrial robot manufacturers mainly provide unit products to complete equipment suppliers. 4. Laser Processing Robots Laser processing robots use robotics in laser processing to achieve more flexible laser processing operations through high-precision industrial robots. The system operates online through the teach pendant and can also be programmed offline. The system produces a model of the workpiece by automatic detection of the machined workpiece, which in turn generates the machining curve, and can also be directly processed using CAD data. Can be used for laser surface treatment of workpieces, drilling, welding and mold repair. 5. Vacuum robots Vacuum robots are robots that work in a vacuum environment. They are mainly used in the semiconductor industry to realize the transmission of wafers in vacuum chambers. Vacuum robots are difficult to import, are limited, use a large amount, and have strong versatility. They have become a key component that restricts the progress of R&D of semiconductor equipment and the competitiveness of the entire product. Moreover, foreign countries have rigorously reviewed Chinese buyers and belonged to the embargoed product catalog. Vacuum manipulators have become a serious problem that restricts the manufacturing of semiconductor equipment in China. Direct-drive vacuum robot technology belongs to original innovation technology. 6. Clean Robots Clean robots are industrial robots that are used in a clean environment. With the continuous improvement of production technology, the requirements for the production environment are increasingly demanding. Many modern industrial products are required to be produced in a clean environment. Clean robots are the key equipment needed for production in a clean environment. Industrial robot applications Typical applications for industrial robots include welding, painting, assembly, collection and placement (eg, packaging, palletizing, and SMT), product inspection, and testing; all work is done with efficiency, durability, speed, and accuracy. 1. The conveyor line robot and conveyor line logistics automation system is mainly composed of the following components: automated conveyor line, robot system, automated three-dimensional storage supply system, main line control system, bar code data collection system, product automation test system, production line monitoring / Dispatch / Management System. Robot and conveyor line logistics automation system can be applied to building materials, home appliances, electronics, chemical fiber, automobile, food and other industries. 2. Glue The robot gluing station is a robot application system developed and developed by the robot center. It mainly includes robots, glue supply systems, glue spreaders, workstation control systems, and other peripheral ancillary equipment. The workstation has a high degree of automation and is applicable to many varieties and mass production. It can be widely used in automotive windshields, automobile and motorcycle headlights, building materials doors and windows, solar photovoltaic cell coating and other industries. 3, welding The system is generally more commonly used gas metal arc welding (MIG, MAG, CO2 welding) or non-gas metal arc welding (TIG, plasma arc welding) method. Equipment generally includes: welding power supply, welding torch and wire feeding mechanism, welding robot system and corresponding welding software and other auxiliary equipment. Automatic robot welding workstations can be widely used in railway, aerospace, military, metallurgy, automotive, electrical and other industries. 4. The automatic crating robot automatic packing and palletizing workstation is an integrated system, which includes industrial robots, controllers, programmers, robot hand grippers, automatic demolition/stacking machines, pallet transport and positioning equipment and yards.åž› mode software. It is also equipped with automatic weighing, labeling and inspection and communication systems, and is connected with the production control system to form a complete integrated packaging production line. Automatic robot packing and palletizing workstations can be applied to building materials, home appliances, electronics, chemical fiber, automobiles, food and other industries. 5. The automatic welding shaft automatic welding station is used for welding various workpieces with the rotating shaft as the base (a number of cantilevers are placed on it). It consists of a welding robot, a rotary duplex positioner (a number of stations) and a fixture. The use of different fixtures in the same workstation can realize automatic welding of various types of shafts, and the relative position accuracy of the welding is high. Can be widely used in high-quality, high-precision welding of various types of workpieces based on the shaft, suitable for electric power, electrical, mechanical, automotive and other industries.
Stud Triac is developed on the basis of common thyristors. It can not only replace two thyristors with reverse polarity in parallel, but also requires only one trigger circuit and is an ideal AC switch device. . Its English name TRIAC is the meaning of the triac.
China leading manufacturers and suppliers of Stud Triac,Ir Stud Triac, and we are specialize in Stud Type Triac,Sc108 Data Triac Stud, etc.
Stud Triac,Ir Stud Triac,Stud Type Triac,Sc108 Data Triac Stud
YANGZHOU POSITIONING TECH CO., LTD. , https://www.cnpositioning.com