Temperature is a major issue in automotive light-emitting diode (LED) headlamps and taillights. Driving the LED with a strong current to produce the necessary brightness may expose it to high ambient temperatures. Combined with a powerful operating current, these high ambient temperatures will increase the LED junction temperature, which typically can only reach 150 °C. High junction temperatures (especially those that violate the data sheet specifications) can damage and shorten LED life. So how do you reduce the junction temperature of the LED?
Equation 1 below represents the electrical power consumed in each LED:
Where Vf represents the forward voltage of the LED and ILED represents the current through the LED. Equation 2 is the general formula of junction temperature:
Where TJ represents the junction temperature, TA represents the ambient temperature, and θJA represents the LED junction measured in degrees Celsius/watt to ambient thermal resistance.
Substituting the electric power equation into the junction temperature equation yields the following equation:
LED forward voltage and thermal resistance are characteristics of LED packages . Therefore, at different ambient temperatures, the LED current is the only control parameter that can be used to verify that the LED junction temperature will not violate the maximum specifications.
In order to change the current through the LED, it is necessary to feed back the ambient temperature measurement to the drive circuit of the LED. Designers often use a negative temperature coefficient (NTC) thermistor to measure the ambient temperature. Specifically, these NTC thermistors change their resistance as the ambient temperature changes, so the designer can measure the voltage on the NTC thermistor and convert that measurement to temperature.
However, a major problem with NTC thermistors is that their resistance will decrease nonlinearly with increasing temperature. In addition, since the resistance is nonlinearly reduced, its current consumption will increase exponentially in temperature. Since the current through the LED is linearly proportional to the temperature, the use of a non-linear device requires some external circuitry or microcontroller to linearize the NTC thermistor voltage and properly adjust the current through the LED.
An analog output temperature sensor integrated circuit (IC) such as TI's LMT87-Q1 generates voltages that are tracked using ambient temperature, simplifies the overall temperature measurement circuit, and enables you to achieve a linear thermal foldback curve. The temperature sensor output can be fed back directly to the device that produces the LED current, eliminating the need to add external circuitry or a microcontroller to linearize the NTC thermistor output. This means that the implementation of thermal foldback does not require a microcontroller and uses fewer components.
Figure 1 compares the use of the NTC thermistor and analog temperature sensor methods. Figure 2 shows the nonlinearity of the NTC thermistor voltage compared to the LMT87-Q1 output voltage.
Figure 1: NTC Thermistor Thermal Foldback vs. Analog Temperature Sensor Thermal Foldback Solution
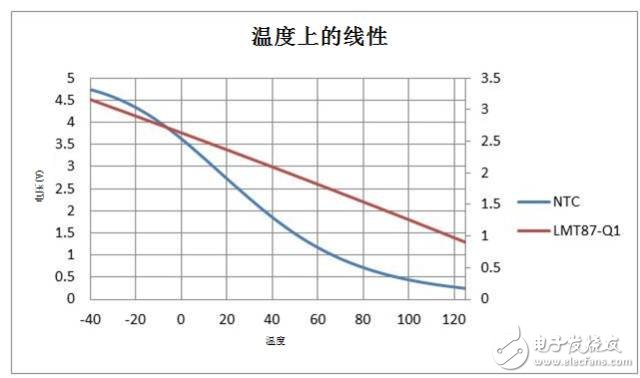
Figure 2: Voltage input at temperature to LED driver
Figure 2 shows the voltage difference across the NTC thermistor and the output voltage of the LMT87. The NTC thermistor voltage was calculated by connecting an NTC thermistor in series with a 10kΩ resistor and connecting the NTC thermistor to a B25/85 of 3435K and a R25 of 10kΩ.
Although it is important that the thermal foldback does not violate the junction temperature, thermal foldback can cause the LED brightness to change. Brightness refers to how bright the LED is actually. LEDs have a thermal down-conversion feature, which is basically a reduction in light efficiency at high temperatures. Although not completely in violation of its maximum specifications, allowing LEDs with high junction temperatures may result in lower brightness than expected or when needed.
Another major factor in LED brightness is the optical components used in the lighting module. Therefore, when thermal foldback requires linear operation, we may need to clamp the curve clamps to different positions. All of these kinetic knowledge must be considered when designing a system for thermal reentry.
Marine Generator with marine diesel engine, marine alternator, control system
. World famous brand marine diesel engine: Cummins, Yuchai, Weichai
. World famous brand alternator: Stamford, Leroy Somer, Marathon, Mecc Alte, Faraday
. Marine control system: Deepsea, ComAp, Deif, SmartGen
. Water Heat Exchanger Type cooling system
Marine Engine,Marine Genset,Marine Generator,Marine Engine Generator
Guangdong Superwatt Power Equipment Co., Ltd , https://www.swtgenset.com